In our mixing equipment, we have achieved stable production by using similar vacuum emulsification cauldrons for a variety of mixing volumes.
We are able to handle a variety of container forms as an OEM, and have built a production structure able to respond to customers' diverse requests.
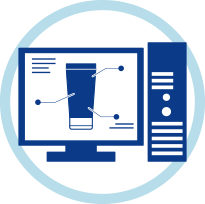
Production control system
Handing off the baton from the R&D Group to the production site
Formulations, specifications, etc. created by the R&D Group are registered in the production control system, as the next step toward implementation at the production site.
Based on the order from the customer, we create a production schedule, order ingredients and containers in the required amounts, and perform system management using bar codes for lots and quantities.
Following the production schedule, we instruct the Mixing Group regarding the type, lot, and amounts of necessary ingredients, and provide information to the weighing system.
Mixing
Assured technology and passion
We eliminate errors through use of the weighing system, to provide peace of mind to customers. (Bar code management: A system by which weighing tolerance is set to zero grams, and the ingredient name/lot does not proceed to the next weighing unless the weight is precisely according to instructions.)
Our vacuum emulsification cauldrons can handle volumes of 200L-1,000L for hair coloring products and 300L-6,000L for hair care products, to meet the needs of customers.
Views of the mixing area
Vacuum emulsification equipment
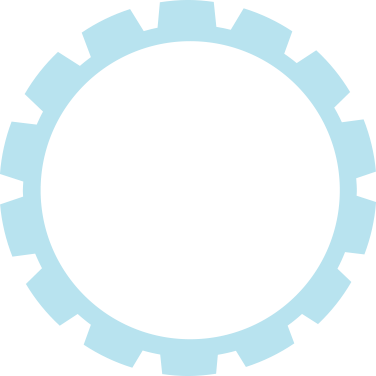
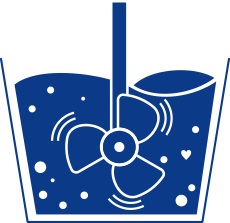
Production control system
Error-free production setup (containers setup/filling and packaging)
Following the production schedule, the production control system issues error-free instructions for materials registered in the system, including the boxes and containers necessary for production, to the containers Setup Group. Following specifications documents, we perform setup of containers shipped from the system-connected automated warehouse.
We issue instructions regarding type, lot, and quantity of containers necessary for production to the Filling and Packaging Group, and issue bulk product shipping instructions for production to the automated bulk product warehouse control system.
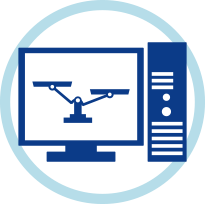
Filling/packaging
We fill products for customers, with love included
We fill containers with bulk product. We use filling equipment matched to container form, selecting the optimal equipment matched to bulk product state and to customers' specifications for production lot, etc.
Liquid filling line
This line is for filling liquid or low-viscosity products such as shampoo, conditioner, and permanent wave liquid. We are equipped with filling equipment for a variety of container forms and volumes.
Hair coloring product filling line
We have 11 production lines for professional-use hair coloring products. We are able to adapt to a wide range of customer needs, with line speeds from medium to high. To maintain quality, inspection cameras on all lines stop the lines upon detecting abnormalities, allowing us to prevent foreign matter contamination and to deliver safety and peace of mind to customers.
Other filling equipment
We have three types of polyethylene tube filling equipment (ultrasound, hot air, and heat sealing), as well as cream filling equipment, four-way laminators, and other types of equipment to meet customers' needs.
Packaging equipment
The packaging equipment for our hair coloring product line includes fully-automated and semi-automated cartoners, which we use in accordance with production lot number and type of cosmetic packaging. In addition, we are equipped with shrinkwrap machines.
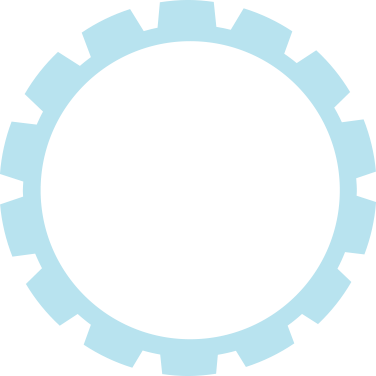
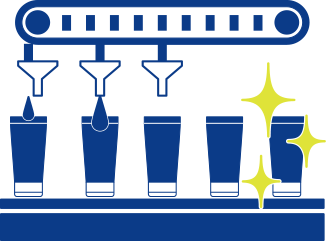
Quality engineering/production control systems
Careful storage of products and bulk products after close inspection
The Quality Engineering Group performs sampling during all bulk product mixing.
Bulk products that have passed all criteria for physical property value testing, bacterial inspection, etc. are managed and stored in the automated high-rise bulk product warehouse, which is linked to the production control system for bulk product names, quantities, and lots.
We also sample all products during production, confirm appearance, specifications, and lot, and manage and store the products in the production control system-linked automated high-rise product warehouse until shipping.
